Then, now and next: Making a mark on materials

Polymers at Polytechnic
Few names loom as large in science as Herman F. Mark, founding director of the Polymer Research Institute and a groundbreaking figure in the study of polymers — extremely important substances made of giant molecules formed by uniting simple molecules, or monomers, by covalent bonds.
Mark was forced to flee Germany in 1938 to escape Hitler’s impending takeover. His lengthy journey eventually took him to the United States, where he accepted a position in 1942 as an adjunct professor of chemistry at what was then known as the Polytechnic Institute.
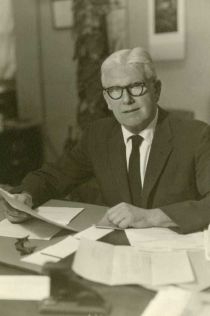
Herman Mark
In 1946, Mark found the Polymer Research Institute. The study of synthetic polymers was at its infant stage in America when Mark formed the Institute. As late as the early 20th century, many of the world’s most prominent chemists resisted the concept of macromolecules.
Today, thanks to Mark’s research and influence, scientists have a vast understanding of polymers. Polymers have high molecular weights, which give them useful characteristics such as high viscosity, elasticity, and great strength. It is through the study of polymers that innovative fibers such as polyester, spandex, and Kevlar were later developed.
The Institute became world-renowned, drawing students and postdoctoral fellows from around the globe, and laying the foundation for materials exploration that continues at NYU Tandon to this day. In addition to creating the Institute, Mark also founded the first American polymer journal, the Journal of Polymer Science, in 1946.
Getting oil out of plastics ….
Frito Lay famously had to do away with their biodegradable Sun Chip bags in 2010. The reason: when crinkled, the bags made noise as loud as 95 decibels — about as loud as a motorcycle. Most consumers clearly expected earth-friendly products to perform like the traditional products they’re used to. That was especially true in fields like plastics, which are traditionally based on petroleum. That problem is where Richard Gross (‘86) came in.

After graduating from Poly, Gross became a member of our faculty, and began developing an improved, bio-based alternative to petroleum-based plastics that could be used in everything from bottles to garment bags.
The method Gross created produced a strong, highly ductile bioplastic using yeast. The Journal of the American Chemical Society published Gross’s findings in 2010. His method involves a fairly quick, relatively low-cost way to use engineered yeast to make large quantities of omega-hydroxyfatty acids from fatty acids of plant oils. When strung together, the acids form a plastic-like polymer.
Gross also partnered with DNA 2.0, a biotechnology company specializing in gene synthesis, to develop enzymes that can both synthesize and break the fuel-latent plastic down into biodiesel after its use.
… And getting coal out of chemical manufacturing
With so many of the items and materials we interact with in our daily lives — from soaps and fertilizers to pharmaceuticals to petrochemicals — deriving from products of the chemical industry, the sector has become a major source of economic activity and employment for many nations, including the United States and China. But as the global demand for chemical products continues to grow, so do the industry’s emissions.
Now, a new research organization has arisen to tackle the most daunting task looming over the industry: how to make industrial chemistry — especially petrochemistry — greener and more sustainable, partly to meet the escalating demands of these greenhouse emission regulations. The multi-institutional effort is called “Decarbonizing Chemical Manufacturing Using Sustainable Electrification,” or DC-MUSE, founded at the NYU Tandon School of Engineering and encompassing a number of schools and institutions.

Led by Center Director André Taylor, the organization is taking the first step in overhauling the chemical industry, moving away from thermally-driven chemical reactions and separation processes that require heat from fossil fuel combustion and moving towards reactions that use electricity generated by renewable resources, like wind and solar.
As part of DC-MUSE’s research, researchers like Miguel Modestino are using his lab’s expertise in composite materials development, processing and characterization to improve and redefine electrochemical reactors.
Shine like diamonds
The colloidal diamond has been a dream of researchers since the 1990s. These structures — stable, self-assembled formations of minuscule materials — have the potential to make light waves as useful as electrons in computing, as well as a host of other applications. But while the idea of colloidal diamonds was developed decades ago, no one was able to reliably produce the structures. Until 2020, when NYU Tandon researchers made a breakthrough.

Researchers led by David Pine, Professor of Chemical and Biomolecular Engineering, devised a new process for the reliable self-assembly of colloids in a diamond formation that could lead to cheap, scalable fabrication of such structures. The discovery could open the door to highly efficient optical circuits leading to advances in optical computers and lasers, light filters that are more reliable and cheaper to produce than ever before, and much more.
Bioengineering artificial bone
For health researchers, modeling disease is a key part of analyzing potential treatments. But for some types of tissue, cells in a petri dish won't do. Elisa Riedo, Professor of Chemical and Biomolecular Engineering at NYU Tandon, took on one of these challenges: the unique, complex structures of human bone
Riedo is well-known for her pioneering work in thermal scanning probe lithography (tSPL), a novel and sustainable nanofabrication technique with applications in biomedicine, nanoelectronics, and magnetic materials. Among other advancements, tSPL has made it possible for orthopedic researchers to not only create artificial bone tissue that precisely matches the real thing, but to do so in such microscopic detail that it includes tiny structures potentially important for stem cell differentiation, which is key to bone regeneration.

Beyond her work on tSPL, she is widely known for her discovery of the exotic viscoelastic properties of nano-confined water, the development of novel atomic force microscopy methods to study the elastic properties of nanomaterials, and the first observation of the exceptional mechanical properties of diamene – single layer diamond obtained from pressurizing graphene. And in 2022, she even discovered a new law of fiction that could lead to a deeper understanding of energy dissipation in friction and the design of two-dimensional materials capable of minimizing energy loss.
Unstitching the links between clothing and petrochemicals
The startup Sunthetics is harnessing energy from sunlight to fuel the electrochemical and thermochemical reactions necessary to transform plant waste into the precursor materials needed to produce nylon – and much, much more.

It began in 2017, when Professor of Chemical and Biomolecular Engineering Miguel Modestino garnered a Global Change Award from the H&M Foundation for a proposed method of using water, plant waste, and solar energy to manufacture nylon, instead of the fossil fuel currently used. Two of his students, Myriam Sbeiti and Daniela Blanco joined forces to launch Sunthetics, in order to shepherd that innovation from the lab to the real world. They envision the process being of interest to not just the fashion industry – which produces millions of tons of petrochemical-based nylon each year, thereby generating significant emissions of carbon dioxide – but to anyone in the broader chemical-manufacturing world seeking greener production methods.
Blanco was even featured in the National Geographic special “Own the Room,” following her competition in the Global Student Entrepreneur Awards.