Researchers Show How Syntactic Foams can be Produced for Cars and Consumer Goods

A computer model showing hollow particles filled in a matrix
Syntactic foams — strong, exceptionally light materials made of plastic perfused with hollow microspheres — are used in everything from buoys and boat hulls to soccer balls and solid rocket boosters. Because they weigh less than molded plastic components, they are now making their way into new industries, including the automotive sector and consumer products.
But producing syntactic foams at industrial scale is a challenge because the microspheres tend to break during the mixing process, which increases the density of the final product, thereby reducing its key advantage. This is why, while there are dozens of manufacturers of plastic precursors, such as polyethylene, polystyrene and vinyl, and several of microspheres, few companies can make syntactic foam, especially of molded thermoplastics, at industrial volumes.
Researchers from the NYU Tandon School of Engineering collaborated with the National Institute of Technology-Karnataka (NIT-K), India, to study the means by which smaller plastic components manufacturers can create these strong, light compounds by mixing hollow microspheres into molded plastic products. Thanks to a collaboration with an industrial partner in India, the team proved that the materials can be produced with economies of scale by smaller companies for automotive and consumer products sectors.
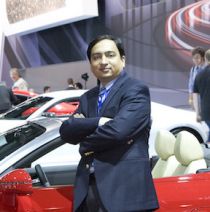
Associate Professor Nikhil Gupta
In research published in the Elsevier journal Composites Part B, the team — which included Nikhil Gupta, an associate professor at NYU Tandon, and Mrityunjay Doddamani, an assistant professor of mechanical engineering at NIT-K — developed a compression-molding-based processing method for syntactic foam comprising of glass microballoons or fly ash cenospheres permeating high-density polyethylene. Achieving a 36 percent weight reduction in these plastics while conferring better mechanical properties, the researchers were able to make components lighter and cheaper, while reducing their manufacturing carbon footprints.
“At laboratory scale, when you are mixing components in a flask, you can be careful and minimize damage,” said Gupta. “But at an industrial scale, producers have to make large quantities of material quickly, because time is money. Thus, breakage of these particles becomes much more problematic. This was one of the major challenges we wanted to solve in this study with India.”
— Dean Katepalli R. Sreenivasan
To minimize microsphere fractures, the team developed parameters for use by small operations with industrial injection molding machines. After Gupta performed the mathematical modeling necessary to find optimal mix ratios, the researchers turned to India’s abundance of small-scale manufacturers who employ plastic molding equipment to test the concepts. The team then collaborated with the manufacturers to fine-tune mixing parameters.
“Industry participation can significantly reduce the entry barrier for development of new materials,” added Gupta. “And with many small-scale industries supplying parts to major manufacturers, India is well poised to benefit from the new technologies.”
“Sophisticated, light-weight materials, such as syntactic foams, are key to making today’s cars and trucks more efficient, regardless of whether they run on gasoline or electricity,” said Katepalli R. Sreenivasan, Dean of the NYU Tandon School of Engineering. “But for automakers and other manufacturers to employ these composites they must be readily available at industrial volumes, something that NYU Tandon and the National Institute of Technology have demonstrated is feasible today. Because these light-weight components confer cost and energy benefits while lowering the carbon footprint of suppliers, automakers, and consumers alike, this research could lead to windfalls not just for industry, but for society as a whole.”
“This project is an excellent example how cutting edge materials technology jointly developed between India and the USA will benefit many industries in India,” said K. Uma Maheshwar Rao, Director of NIT-K.
With the help of industry, the research team now plans to extend the work to cast prototype components and to test them in actual applications.